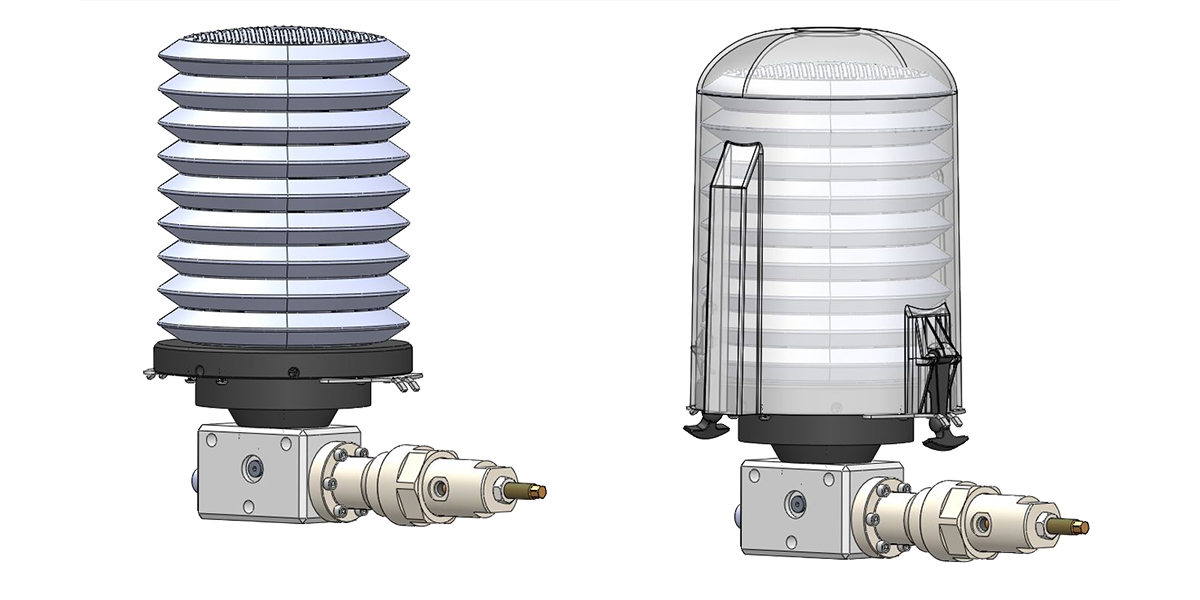
Installing automatic grease systems on heavy machinery is a smart business move that can save money and reduce labor costs in the long run. An automated grease system is designed to provide consistent, reliable lubrication for moving parts of industrial equipment, helping them last longer and work more efficiently.
This type of system uses multiple components to deliver precise amounts of lubricant at specific intervals throughout a machine’s runtime. The result is reduced wear on machinery components and smoother operation overall. An automatic grease system requires minimal human intervention once it's installed and set up properly.
This means businesses can lower their maintenance expenses while still ensuring their machines are well lubricated, with no downtime due to unexpected malfunctions or repairs.
What Makes the Best Automatic Greasing System?
There are five qualities that an automatic grease system should have to optimize machine performance:
- Reliability
- Resistance to wear and tear
- Automation
- Consistency
- Customization
1. Reliability
The reliability of an auto grease lubrication system for heavy machinery is paramount to the longevity of the machines and the safety of those using them. Without a reliable system, machines can easily become over-greased or under-greased, leading to a wide variety of issues such as:
- Accelerated wear and tear
- Decreased efficiency
- Dangerous lubricant spills
By using reliable automatic grease systems, companies can ensure their machines will perform at optimal levels for many years - with minimal maintenance required. This slashes operating costs while ensuring the safety of those using the machines.
Automatic grease systems are designed to be easily serviced and maintained so that any issues can be quickly addressed and rectified.
2. Resistance to Wear and Tear
Grease companies use high-quality materials and components in their automatic greasing systems to make sure they’re reliable over long periods of time. This includes using corrosion-resistant materials to withstand extreme weather conditions, salt, and road grime. Equipment parts stay adequately lubricated and warm to facilitate better operation and reduce risk of metal-to-metal contact.
3. Automation
Automation ensures reliable and safe operation of the machines. Automated grease systems can be integrated into the machine itself, eliminating the need for external power sources. This not only reduces the need for manual labor, but also increases the efficiency of operations since it eliminates the potential for human error.
The use of automation also reduces the risk of injury, as workers are not required to grease components manually and can instead operate machinery from a safe distance. Automation also makes it easier for maintenance staff to troubleshoot, because they can easily access the control systems remotely or with diagnostic tools.
4. Consistency
Without a reliable and consistent system, machines can quickly become over-greased or under-greased, leading to decreased efficiency and increased wear and tear. This not only impacts the machine’s life expectancy, but also can lead to dangerous lubricant spills.
By using a reliable auto greaser, companies can ensure their machines will perform at optimal levels for many years with minimal maintenance required. This significantly reduces operating costs, while also ensuring the safety of those using the machines.
Unlike manual lubricating, which can be too liberal or conservative, automated systems are programmed with precision to ensure an exact amount of lubricant is applied every time.
Consistent lubrication will reduce waste and keep equipment running.
5. Customization
One size does not fit all when it comes to greasing systems for heavy equipment, due to factors that impact reliable performance over time.
The good news: many automatic lubrication systems companies offer customizable solutions tailored to the specific needs of each customer’s machinery.
Customizing an automatic lubrication system can provide numerous benefits, from improved reliability and efficiency to reduced maintenance costs. A customized solution can be designed specifically for your machinery by taking into account:
- Machine type
- Lubricant requirements
- Environmental conditions
For example, automated lubrication systems are designed to be easily installed and serviced, allowing companies to quickly get up and running with minimal disruption.
Moreover, automatic lubrication companies offer remote access or monitoring features to diagnose any issues with the system; ultimately reducing downtime and helping to ensure reliable performance.
Automatic Grease Systems | Advancing the Process to Improve Productivity
Overall, automatic grease systems offer a reliable and cost-effective means of lubricating heavy machinery components. The systems are designed to last for many years, require minimal maintenance, and can help companies save money by increasing productivity and reducing the risk of injury due to manual labor.
By automating the greasing process, companies can save time and resources that would otherwise be spent on manual greasing tasks. Automation is meant to help you keep pace in the industrial world, making automated grease systems a must-have.
Improve Efficiency Today
Automatic grease systems have an immediate impact on the operation of the machinery it lubricates and overall job performance. Get in touch with our team today to find your ideal solution.