7 min read
Custom Automatic Oilers and Grease Bank Systems for Farm Equipment
LubeMinder Team
:
Aug 1, 2024 2:46:34 PM
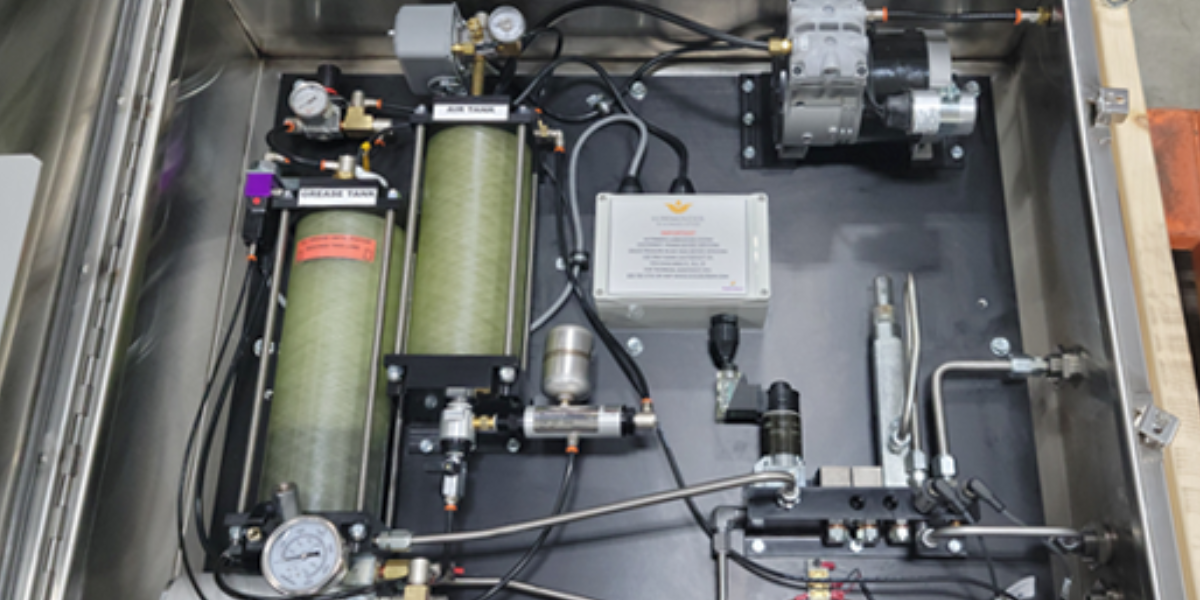
You’ve seen farm equipment that’s out of commission, perhaps more often than it’s in use, struggling through jobs with creaky, under-lubricated parts. It’s not efficient or cost-effective.
You may also have encountered machinery where over lubrication leads to excessive grease and oil, leaving a mess and waste.
When maintaining farm equipment, you don’t have to choose between over-lubricating and under-lubricating. Custom automatic lubrication systems, including automatic oilers and grease bank systems, offer the perfect balance delivering the right amount of lubricant at the right time.
In this article we'll discuss:
- 2 Types of Automatic Lubrication Systems
- Key Considerations
- Core 4 Benefits of Custom Lubrication Systems
- An Auto Greaser Boosts Your Bottom Line
- Reduce Long Term Operational Costs
2 types of automatic lubrication systems
Maintaining farm equipment is a demanding task, especially when it comes to lubricating tools. Over-greasing can lead to waste, while under-greasing can cause premature wear and costly breakdowns/disruptions. To tackle these challenges, the agricultural industry has turned to two innovative solutions:
- Automatic oilers
- Grease bank systems
Automatic Oilers
Automatic oilers deliver precise amounts of lubricant to machinery components at regular intervals to keep smooth operations going and reduce wear and tear. The key benefits of using automatic oilers include:
- Extended equipment life
- Decreased maintenance costs
- Improved operational efficiency
These systems automate the lubrication process, minimize manual intervention, maintain consistent lubrication, and reduce the risk of human error.
In the agricultural industry, automatic oilers are commonly used in various farm equipment, such as hay balers and combine harvesters. These systems help maintain the optimized performance of engines, gearboxes, and other moving parts, which are important for the effective functioning of farm machinery. Making sure these components are properly lubricated, automatic oilers aid in increasing productivity and reducing downtime during peak farming seasons.
Did you know that automatic oiling systems are the best way to prevent chain failure?
Read here to know the top 3 causes of chain failure and how to prevent them.
Grease Bank Systems
Grease bank systems focus on the lubrication points of machinery, allowing for multiple components to be lubricated from a single location. This setup not only simplifies the maintenance process but also makes sure the right amount of grease is applied to each part, reducing wastage and improving machinery performance.
Grease bank systems are extensively used in various types of farm equipment. These systems are valuable in equipment with numerous lubrication points, where a conventional lubrication system would be time-consuming and more likely to cause errors. Grease bank systems help ensure the main parts get enough grease, keeping farm machinery reliable and efficient.
Feature | Automatic Oilers | Grease Bank Systems |
---|---|---|
Lubrication Method |
Deliver a continuous flow of oil to necessary components |
Provide grease at specific intervals, typically involving manual activation |
Maintenance |
Lower maintenance due to less frequent checks and refills required |
Higher maintenance is needed to check and refill grease points regularly |
Ease of Use |
There is less hands-on interaction; systems often have remote monitoring and control capabilities |
More manual interaction and monitoring are required to ensure all points are adequately lubricated |
Precision |
High precision in lubricant delivery, ensuring each part gets just the right amount of lubrication without waste |
Less precise can lead to over or under lubrication if not monitored closely |
Effectiveness in Dirt |
Oil systems can attract and collect more dirt and debris, which may require more frequent cleaning of the oil reservoir |
Grease provides a seal at lubrication points, which helps prevent dirt and debris from entering |
Initial Installation Cost |
Generally higher due to the complexity of the system and components involved |
Lower initial costs as the systems are less complex |
Operational Costs |
Lower operational costs over time due to reduced wear and tear and the efficiency of the lubrication process |
Potentially higher operational costs due to less efficient lubrication and more frequent maintenance |
Environmental Impact |
Oil systems require careful handling and disposal to prevent environmental contamination |
Greases systems, while also needing proper disposal, typically have less spillage and can be easier to manage |
Durability in the Field |
Susceptible to damage from harsh environmental conditions which can affect system integrity and function |
More robust in harsh conditions, with less vulnerability to damage from dirt, water, and field debris |
System Complexity |
A more complex system with higher requirements for system integrity and clean oil |
Simpler systems with less stringent requirements on cleanliness and system integrity |
Don't get stuck: Key considerations when choosing your custom lubrication system
Understanding where and how it will be important to implement a lubrication system in your farming equipment helps reduce maintenance costs and time. Here are some key considerations to think about when choosing between an automatic oiler and grease bank system for your farm equipment:
- Equipment compatibility
- Assessing lubrication needs
- Identifying high wear and tear areas
- Determining the right system capacity
- Customization options for different equipment
- System dependability in environmental conditions
- Material quality and construction
- Ease of installation and maintenance
- User-friendly design features
Equipment Compatibility
Each type of farm equipment, such as hay balers and combine harvesters, may have unique lubrication needs and components. Assessing these requirements helps select a system that will provide optimal lubrication and enhance machinery performance. Additionally, compatibility confirms that the system can be easily integrated into existing equipment without major modifications.
Assessing Lubrication Needs
For example, hay balers and combine harvesters have multiple moving parts that require consistent lubrication. Evaluating these needs involves understanding the machinery's operational demands and identifying the components that are most susceptible to wear and tear. By considering these factors, workers in the farming industry can select an automatic oiler or grease bank system that meets the unique needs of their equipment to maintain reliable performance.
Identifying High-Wear Areas
High-wear areas are machinery parts that experience significant friction and stress during operation. Regularly lubricated high-wear areas will cause reduced wear and a longer lifespan for the equipment. Automatic oilers and grease bank systems can be programmed to provide more frequent lubrication to these areas, making sure they are adequately protected and reducing the risk of breakdowns or costly repairs.
Determining the Right System Capacity
The capacity of the lubrication system should be sufficient to meet the demands of the equipment it services. This includes considering the volume of lubricant required and the frequency of lubrication cycles to avoid under or over-lubricating components. It's essential to pick a system with enough capacity, so all moving parts receive the right amount of power. This will reduce costs later down the road when an upgraded lubrication system or a broken piece of equipment needs to be replaced.
Customization Options for Different Equipment
Customizable systems can be tailored to fit specific machinery requirements, ensuring comprehensive and efficient lubrication. This is particularly useful for farmers who have a diverse range of equipment and need a system that can cater to different lubrication needs.
System Dependability in Environmental Conditions
Farm equipment operates under varied environmental conditions, from dusty fields to wet and muddy terrains. When choosing your automatic oiler or grease bank system, keep in mind it must be robust while providing consistent performance. It is essential to select a system from a reputable manufacturer that offers high-quality components and has a proven track record for reliability and longevity.
Material Quality and Construction
The quality of materials used in building automatic lubrication systems impacts their performance and longevity. Systems made from high-quality, durable materials are more likely to offer reliable service over extended periods and under challenging conditions. Additionally, the type of lubricant used in the system should also be considered, as certain materials may not be compatible with specific types of grease or oil.
Ease of Installation and Maintenance
A user-friendly design facilitates easy installation and maintenance is advantageous. Systems that are straightforward to install and require minimal maintenance can save time and reduce the labor costs associated with their upkeep. Additionally, the system should have a clear and accessible interface to enable users to monitor its performance and address any issues promptly.
User-Friendly Design Features
Design features promote ease of use, such as clear indicators, accessible grease points, and simple control interfaces, enhancing the user experience. Such features ensure the lubrication system is easy to operate and manage, even for those with limited technical expertise. A user-friendly design also minimizes the risk of errors when using the system, reducing downtime and maintenance costs.
Maintenance Requirements and Long-Term Upkeep
Understanding the maintenance requirements and long-term upkeep of the lubrication system is essential. Systems that require minimal maintenance but offer reliable performance over time are preferable. This not only reduces downtime and maintenance costs but also maintains the continuous efficient operation of farm equipment. When deciding to consider the system's long-term maintenance requirements, choose one that meets the farm's specific needs and budget.
Discover cutting-edge solutions for your manufacturing needs!
Download LubeMinder’s catalog now to take your operations to the next level.
Core 4 Benefits of Custom automatic Lubrication Systems
Custom automatic lubrication systems are designed to meet the specific needs of farm machinery, so each component receives the right amount of lubrication. There are 4 key benefits to custom automatic oilers and grease bank systems:
- Reduced wear and tear on components
- Lower maintenance and labor costs
- Enhance operational efficiency
- Continuous lubrication for optimal performance
Reduced Wear and Tear on Components
By providing lubrication to high-wear areas, custom systems can target to minimize the wear and tear on certain components. Improving the performance of machinery and preventing parts from breaking down leads to increased reliability and operational efficiency. Precision in lubrication makes sure each component receives the correct type and amount of lubricant exactly when it is needed. This precise application reduces friction, heat, and overall stress on moving parts, resulting in a lower rate of breakdowns.
Lower Maintenance and Labor Costs
One of the most significant advantages of using custom automatic lubrication systems is the reduction in maintenance costs. With consistent and accurate lubrication, machinery parts experience less wear and tear, which leads to fewer breakdowns and repairs. The need for frequent manual lubrication interventions is also minimized, freeing up labor resources and reducing downtime. Additionally, the extended lifespan of lubricated parts means that replacement frequencies are diminished, resulting in lower expenditure on spare parts. Over time, the cumulative savings on maintenance and repairs can be substantial, providing a favorable return on investment for the lubrication system.
Enhanced Operational Efficiency
Custom automatic lubrication systems play a key role in maximizing efficiency in farming maintenance equipment. These systems reduce friction between moving components by making sure every component gets the exact lubrication it needs, which lowers resistance and improves functionality. Reduced friction means that the machinery requires less power to function, which results in fuel efficiency and less energy consumption. Optimal lubrication also decreases the heat generated by mechanical operations, preventing overheating to ensure the machinery can perform at its best for extended periods. This consistent lubrication also contributes to the machinery's ability to perform under heavy loads and intense tasks without any breakdowns.
Continuous Lubrication for Optimal Performance
Unlike manual lubrication techniques, where gaps between applications can be missed, custom lubrication systems guarantee the target quantity of lubricant. This continuous flow of lubricant protects against the two main enemies of machinery: wear and corrosion. By providing a constant supply as needed, these systems guarantee that friction surfaces are always well-protected, which minimizes wear and extends the life of the equipment.
an Auto Greaser Boosts Your Bottom Line
In an environment where every minute counts and efficiency is paramount, adopting auto greasers streamlines operations and fortifies a company's competitive edge.
Automating the lubrication process saves considerable time and resources and boosts essential machinery's longevity and efficiency.
With compelling cost savings, uptime improvements, and labor efficiencies, implementing an auto greaser system is one of the smartest investments a facility can make in improving productivity. The system quickly pays for itself while enabling your team to get more done each day.
But wait, there’s more! Discover here the 6 functions and 5 benefits of an automatic lubrication system
Invest Today, Save Tomorrow: Reducing long-term operational costs
By implementing industrial lubrication systems, operators can ensure their machines maintain peak efficiency and reliability throughout the seasons. Similarly, workers and drivers may increase their equipment's lifespan and improve their machines' performance during job assignments.
Considering the right automatic lubrication system for your needs can guarantee that your investment will lead to a more efficient and cost-effective tomorrow.