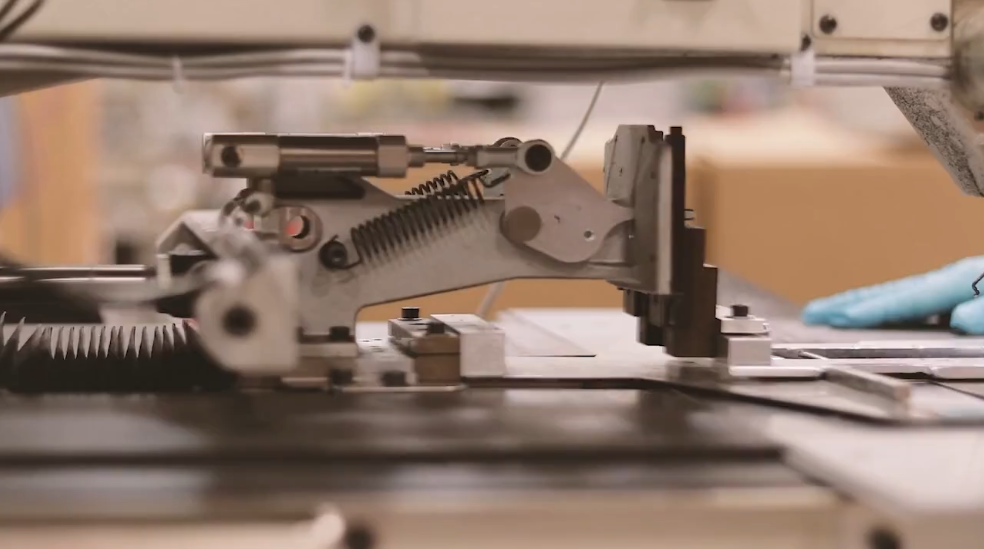
Industrial sewing plays an important role in custom textile manufacturing. In industrial spaces, it's common to have everyday factory, job site, machine, and equipment issues. Yet, there are not a lot of common solutions available to solve the problem. That's where custom textile manufacturing comes in - to solve everyday problems that don't have a solution yet. Sometimes you have to be specific, and cater to a particular vehicle, machine, or piece of equipment down to where the final stitch goes - and industrial textile manufacturers can help streamline the custom part process.
We will be discussing how industrial custom textile manufacturing, works:
- What is Custom Textile Manufacturing?
- What Can You Manufacture With Textiles?
- Examples of Custom Textile Fabric
- The Textile Manufacturing Process
- Premiere Domestic Textile Manufacturer
What is a custom textile manufacturer?
Custom textile manufacturers design, fabricate, and convert materials. An engineering team assists in the designing process, after which the original fabric material undergoes modification into a specific format or product. This transformation is achieved through rotary die cutting, followed by assembly, all of which are carried out by the manufacturing company.
What can you manufacture with textiles?
The sky is the limit when manufacturing textiles - especially for industrial purposes. When working on a job site or in a factory, there are many aspects to consider for improvement. Maybe wires and cords need to be held together, but there isn't a band large and strong enough to keep them together, or they get tangled too often, resulting in restarting machines. When nothing on the market has what you need, custom textile manufacturing comes in. Instead of making an exhaustive list of what textile manufacturers can do, here are some things they have done:
- Bundling straps
- Custom grommets
- Custom straps
- Insulated covers
- Heated covers
- Protective sleeves
- High-temperature covers
- Electric sleeving
- Energy chain covers
And that is just the beginning. If you have an idea, a design team of engineers at a custom textile manufacturer will make it come to life. Or if you have a problem and still need a solution, a manufacturer can come up with the idea, too.
Examples of custom textile fabric
There are a variety of custom textile fabrics, ranging from nylon to vinyl. We will be discussing the most commonly used fabrics in industrial textile manufacturing facilities. Industrial textile fabrics carry unique properties that can't be found in fabric you can find at a local craft store. These are designed to withstand extreme conditions; which makes them ideal for products used in harsh environments.
Fabrics used in industrial custom textile manufacturing and their best characteristics:
The textile manufacturing process
The manufacturing process will vary depending on the capabilities of the manufacturer. In general, you can expect the textile manufacturing process to be composed of four steps:
1. Designing
2. Prototyping
3. Producing
4. Inspecting
Designing a custom textile
The beginning of the manufacturing process starts at design. There are a few ways this can happen:
- You have an idea and the engineering team begins creating blueprints. This process is fairly streamlined. The engineering team asks you questions about your idea, and works with you to create a few standard designs before making a preliminary blueprint.
- You have a problem, but still are unsure what design will fix it. If you still need the solution to be imagined, the engineering team will ask you questions about your problem, and create a few designs that will work to fix the issue. The team will then create designs, tweak them with your help, and create a blueprint to get started. Note: if a manufacturing facility is approached without a general idea first, it may take longer to get the product through.
Once a blueprint is approved and everyone involved likes the idea, it's onto prototyping.
The Custom Prototype
Next, rapid prototyping begins on the custom parts. This is often done with the actual materials that will be on the final product. Depending on the manufacturer and scope of the project, this process can take from a few days to a few weeks to be completed. Once the prototypes are made, they are sent to the customer for approval. If the product is approved, it gets sent to the production floor - if it needs some tweaking, the design and prototype process is revisited until the prototype is approved by the customer.
When the prototype proves to be reliable, the design is sent to the production floor.
Starting Custom Part Production
In production, the product is built and sent to testing before it's packaged away. Depending on the product, there will be different standards and tests it has to pass before it is good to go.
Inspecting The Textile
The last step is inspecting the textile before it gets distributed. The inspection phase requires a variety of tests. For example, a manufacturer may check for durability, the strength of seams, and ensure there aren't any imperfections or holes before the product is placed on a pallet. These practices ensure the customer gets the product they expect from the prototype phase.
Premiere domestic custom textile manufacturer
The process for a custom textile should be worry-free. It's important to keep in mind there will be deviations of the general textile manufacturing process depending on the custom manufacturer you choose. It's also important to speak with each professional you will be working with to determine if its a good fit for you and them; there's no knowing if it'll be a working relationship that lasts for a period of time, or a lifetime.
Having a reliable and professional textile manufacturing company is vital to creating the product you thought up (or need some advice on). If you need it, we can design it. We walk you through the process from ideation to creation, and keep you informed along the way for a no-surprise, communicative experience.
Let's chat so we can make a custom solution perfectly fit for you.