3 min read
How to Reduce Rework with the Right Woodworking Compressed Air System
Tsunami Team
:
Aug 1, 2024 4:12:30 PM
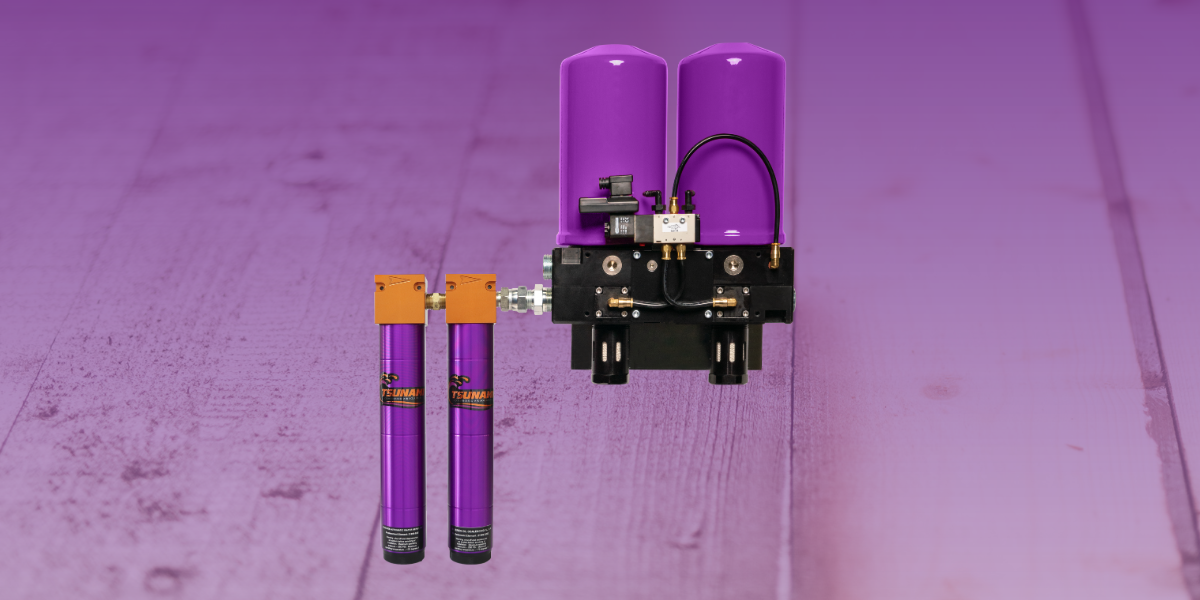
For any woodworking manufacturer, the finishing process is the crucial final step that can make or break a product. A high-quality finish enhances the natural beauty of the wood while providing vital protection against moisture, UV rays, scratches, and wear. However, achieving a flawless finish on a manufacturing scale is an intricate undertaking.
Operationally, achieving a great finish facilitates lean processes by minimizing rework and returns, while boosting throughput. Common challenges to providing this quality completed project include:
- Controlling dust
- Achieving consistent coverage
- Managing complex finish interactions
- Environmental regulations
- Balancing production speed with quality
In this article, we are going to discuss pain points in woodworking and the best solutions in the industry to address them with:
- How the Right Woodworking Compressed Air System Impacts Wood Finishing
- The Problem: Rework and Its Consequences
- The Solution: Compressed Air Dryers
- Implementing a Compressed Air Dryer
- The Path to Perfection: Compressed Air Dryers and Your Wood Finishing Success
How the Right Woodworking Compressed Air System Impacts Wood Finishing
Clean air is important during the prep phase in particular, as it helps remove initial contaminants without adding additional debris to the surface that is about to be finished.
Compressed air delivers consistent power and clean airflow, which is crucial for wood finishing. The right woodworking compressed air system allows production to move forward smoothly and predictably compared to less consistent power sources or production means.
Besides ensuring clean air, compressed air dryers can also tackle another problem in woodworking: moisture. Moisture on wood finishes and coatings can lead to spots on the surface, requiring the finish to be sanded off and redone. This wastes workers’ time that could be more effectively applied elsewhere. With a regenerative dryer installed, the appearance of spots on the finished product can be greatly reduced.
Equipment clogging and rust are also concerns in areas where humidity is high.This not only creates a constant struggle to complete the wood finishing process without defects but also means significant investment in spray gun rebuilds and inventory to ensure reliable equipment is available when needed.
Regenerative dryers deliver a fast return on investment. They efficiently remove moisture and oil from spray gun lines, without needing electricity to operate. Additionally, their simple design with minimal moving parts minimizes maintenance needs, reducing workload for your staff.
Installing a dust collector will also improve system performance and air quality in the work area. This provides a cleaner work environment for production and improved air quality for the employees. You'll save yourself:
- Time
- Money
- Aggravation from the maintenance and downtime that results from dust interfering with machinery operation.
The Problem: Rework and Its Consequences
Debris and moisture are the leading culprits behind rework in wood finishing. Debris in the finish creates defects, while moisture prevents proper sealing and degrades product quality.
Compressed air powers:
- Spray guns
- Pneumatic sanders
- Nail guns
- Other vital tools in the finishing process.
However, contaminants like moisture, oil, dirt, and pipe debris can easily become aerosolized and released from compressed air lines, causing:
- Finish Defects: These imperfections require sanding, resurfacing, and potentially reapplication of the finish, adding significant time and material costs.
- Delayed Deliveries: Rework pushes back completion dates, potentially leading to unhappy customers and strained client relationships.
The Bottom Line: Compressed air quality directly impacts your bottom line. Time lost due to rework means lost revenue, while customer dissatisfaction can damage your reputation.
The Solution: Compressed Air Dryers
Compressed air dryers have been available for over a century. These products are used in several industries.
A point-of-use compressed air dryer provides optimal air pressure for tools in specific shop areas. If those tools need reliable, consistent air pressure, then installing compressed air systems increases shop efficiency and decreases the chance of downtime and production delays. It also provides a longer lifespan for the tools themselves, particularly in areas where high humidity is a constant challenge.
How Do Compressed Air Dryers Work?
Compressed air dryers provide cooled air that is free of humidity and clean of debris that naturally flows through the air in any work environment. For situations like wood finishing, where that debris can significantly impact the finished product, using clean, dry compressed air can go a long way toward greater efficiency.
Pro Tip: For more information, consider reading through this resource: The Rule of 20: Unlocking Efficiency in Compressed Air Systems.
Implementing a Compressed Air Dryer
The right compressed air dryer for your operation depends on:
-
The size of the work area
-
The tools and other equipment that will rely on the compressed air dryer
-
The number of uses the air dryer will be providing dry, clean air to during the work day
-
Electricity needs
-
The complexity of the dryer’s operation process
For a better idea of maintenance schedules and best practices for servicing filters, consider these resources from our blog library:
- How to Service Tsunami Filters
- Servicing Your Regenerative Dryer
- The Case for Scheduled Preventative Compressor Maintenance + Checklist
The Path to Perfection: Compressed Air Dryers and Your Wood Finishing Success
Achieving flawless wood finishes goes beyond just skill and craftsmanship. It requires the right tools, and your compressed air supply is a crucial one.
Investing in the right woodworking compressed air system is essential to reducing rework and meeting delivery deadlines. Appropriate filters, dryers, and other air preparation equipment ensures clean, dry air reaches your tools for optimal operation and finishing results every time.
In fact, installing a compressed air dryer can pay for itself rapidly by preventing costly rework, product rejects, and finish failures. With proper drying, you'll see consistent finishes, reduced disruptions, longer tool life, and greater overall productivity.
From the start of finish prep through the final coating, having the right compressed air solution provides the foundation for wood finishing perfection. This investment ensures not only beautiful results but also satisfied customers who can cherish your work for years to come.