Avoid Contaminates in the Food and Beverage Industry:
Quality Food Grade COMPRESSED AIR
Just like other manufacturing processes, compressed air is used to power conveyors, mixers, sorters and other production equipment. Clean, dry air is required for these processes to keep the machines up and running while improving efficiencies of the facility overall. In the food and beverage packaging industry, compressed air is often necessary to power machinery and ensure packaging meets FDA requirements.
Compressed air in the food industry
‾‾‾‾‾‾‾‾‾‾‾‾‾‾‾‾‾‾‾‾‾‾‾‾‾‾‾‾‾
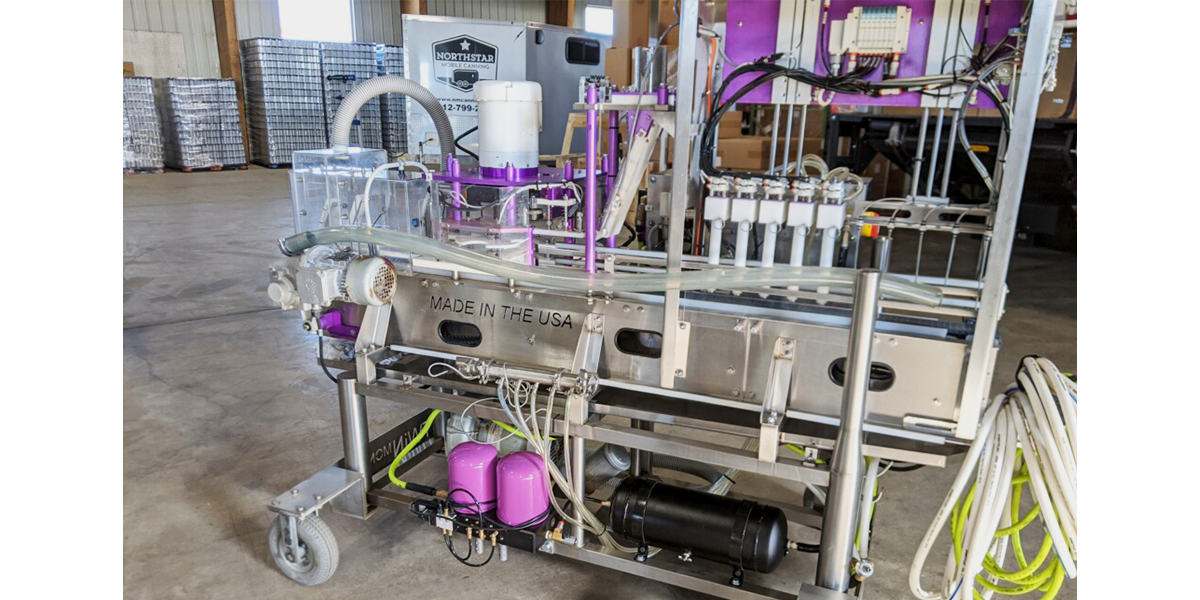
Unlike other manufacturing processes, in the food industry compressed air is used in direct contact with food ingredients. This includes blowing off food debris, and a variety of food packaging machines including: vacuum sealing packaging, carton filling and sealing, meat packaging and dehydrating. Throughout these processes, the air is touching food or other components that come in direct contact with it. Compressed air is used throughout the food and beverage production and food and beverage packaging process.
From product handling conveyors to vacuum sealing, compressed air plays a vital role in bringing food from factory-to-table.
There are two types of air usage in the food industry:
-
Direct Contact: Blowing off produce or forming patties
-
Indirect Contact: Powering the functions of machines like conveyors, mixers etc.
Direct Contact
‾‾‾‾‾‾‾‾‾‾‾‾‾‾
Direct contact applications in the food industry pose a threat to end consumers if the compressed air isn't properly filtered. Oils, particulates and moisture from the air and air pipes can contaminate the food, and deem it unsafe for consumption in accordance to FDA requirements. Examples of direct food contact include:
- Blowing off food debris
- Vacuum sealing
- Carton fill and seal
- Meat packaging and dehydration
Indirect Contact
‾‾‾‾‾‾‾‾‾‾‾‾‾‾
For indirect contact applications, the cleanliness of the compressed air does not pose a threat to the end consumers. These applications use the air to power pneumatic tools and processes within the machinery to complete its function. Some examples of indirect food contact for compressed air include:
- Product handling conveyors
- Ingredient mixers
- Food sorters
- Liquid filling stations
- Roll stock packaging machines
- Case packaging machines
Food Grade Compressed Air
‾‾‾‾‾‾‾‾‾‾‾‾‾‾‾‾‾‾‾‾‾‾‾‾‾‾‾‾‾
Food grade compressed air is compressed air that has met the ISO cleanliness requirements for a specific machine or process. Although there no legal ramifications for the quality of air that is used in these processes, some manufacturers provide the air quality standard for their machines.
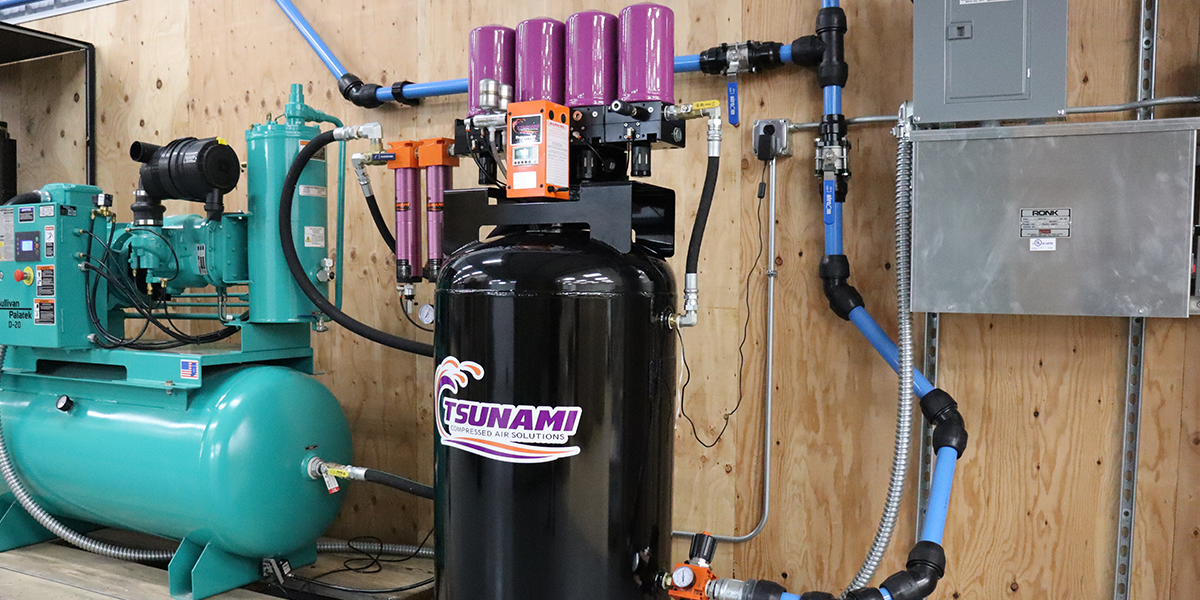
Food Safety for Compressed Air
‾‾‾‾‾‾‾‾‾‾‾‾‾‾‾‾‾‾‾‾‾‾‾‾‾‾‾‾‾
Compressed air standards for the food industry state that air that is in contact with food must be clean and dry for it to be deemed safe. If the air is treated correctly, it is safe to be in direct contact with food or food contact surfaces. Having a food grade compressed air filter on food packaging equipment is recommended when following food safety standards.
The ISO 8573-1 2010 standard provides facilities with guidelines for food safe air. Some food packaging manufacturers will provide the required ISO classification for their machine or application. One particular application, food forming, has a requirement of Class 2 in particles and humidity, and Class 1 for oil contamination. The chart below provides specific guidelines for a compressed air filter for the food packaging industry.
Compressed Air Purity Classification Chart
Source: International Organization for Standardization
Using Compressed Air That Meets Quality Standards:
Contaminant Sources and Benefits
‾‾‾‾‾‾‾‾‾‾‾‾‾‾‾‾‾‾‾‾‾‾‾‾‾‾‾‾‾
Contaminant Sources
- Ambient air containing water, oil, or bacterial parts
- Rusted pipes
- Charcoal filters and canisters with shed particles
- Sealing tape
- Condensed water, liquid, and oil in the system from vapor or aerosol
- Airborne microbes
- Humidity present in the air
Benefits
- Limited microbial and bacterial growth on products and equipment
- Eliminating corrosive particles in sterilized food
- Stopping hazardous ramifications to consumer health
- Absence of accumulation of contaminants in food and beverage products
- Reducing pipe corrosion and increasing the lifespan of filters, drains, and machinery
- Increased manufacturing efficiency, saving time, money, and resources
Your Clean, Compressed Air For Food & Beverage Manufacturing Checklist
1. Assess your air composition quality.
2. Assess the level of moisture in the air.
3. Identify what risks are associated with the results.
4. Determine what controls are in place to remedy this. If there are none, get to work!
5. A compressed air improvement plan, including extra preventative steps to ensure customer safety and increase plant efficiency.