Dry Air for Manufacturing
Known as the “fourth utility”, dry compressed air is a critical component in any manufacturing facility. The vast array of air-powered torque-drivers, pneumatic grippers, air presses, and impact wrenches demand consistently dry air for optimum reliability and service life.
Treating the compressed air in your shop shouldn’t be overlooked, air dryers and filters prevent condensation from degrading the performance of air devices located downstream.
.png?width=500&height=500&name=23224_SMG_Tsunami_AirDryer_pure5-T%20(WEB).png)
The Benefits of Using Dry Air in Plasma Cutting
Plasma cutters are industrial machines that use a combination of gasses and an electric arc to create a “plasma jet”, piercing through solid metals such as mild steel, stainless steel and aluminum. Compressed air is used in precision plasma cutters to produce sharper and higher quality cuts by means of adjusting the air intake for perfect consistency.
Without filtration and drying, compressed air contains impurities including liquid water, particulates, and vapors. Failing to use proper air treatment will inhibit the performance and longevity of the plasma cutter. Other consequences include:
- Shorter life of the plasma consumables, increased costs
- Contributions to torch and machine
- Cuts could appear sloppy, comprising the quality of the final product
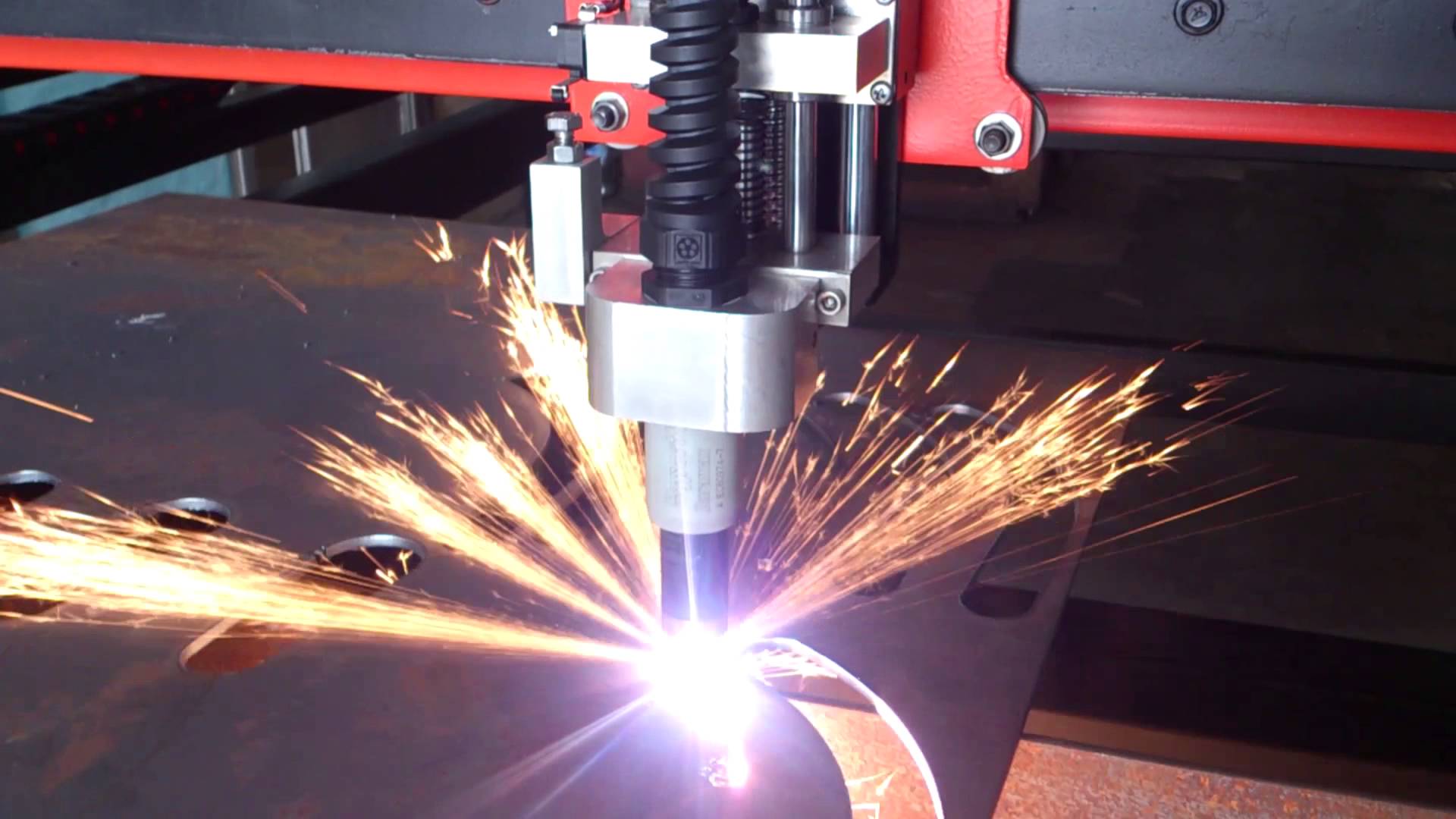
Creating the best sandblasting performance, moisture free
Sandblasting, also known as abrasive blasting, is a surface refinishing process that involves the use of a machine to spray particles against a surface using very high pressure. This process removes any unwanted imperfections and provides a smoother surface for large projects such as pipelines, storage tanks, ships, highway overpasses, bridges and more. These steel infrastructures rely on sandblasting to prevent corrosion and provide a clean surface for coating.
Compressed air is the propellant for pushing the abrasive particles to the surface. Any moisture or unwanted contaminants will cost the operator in productivity and quality of the job.
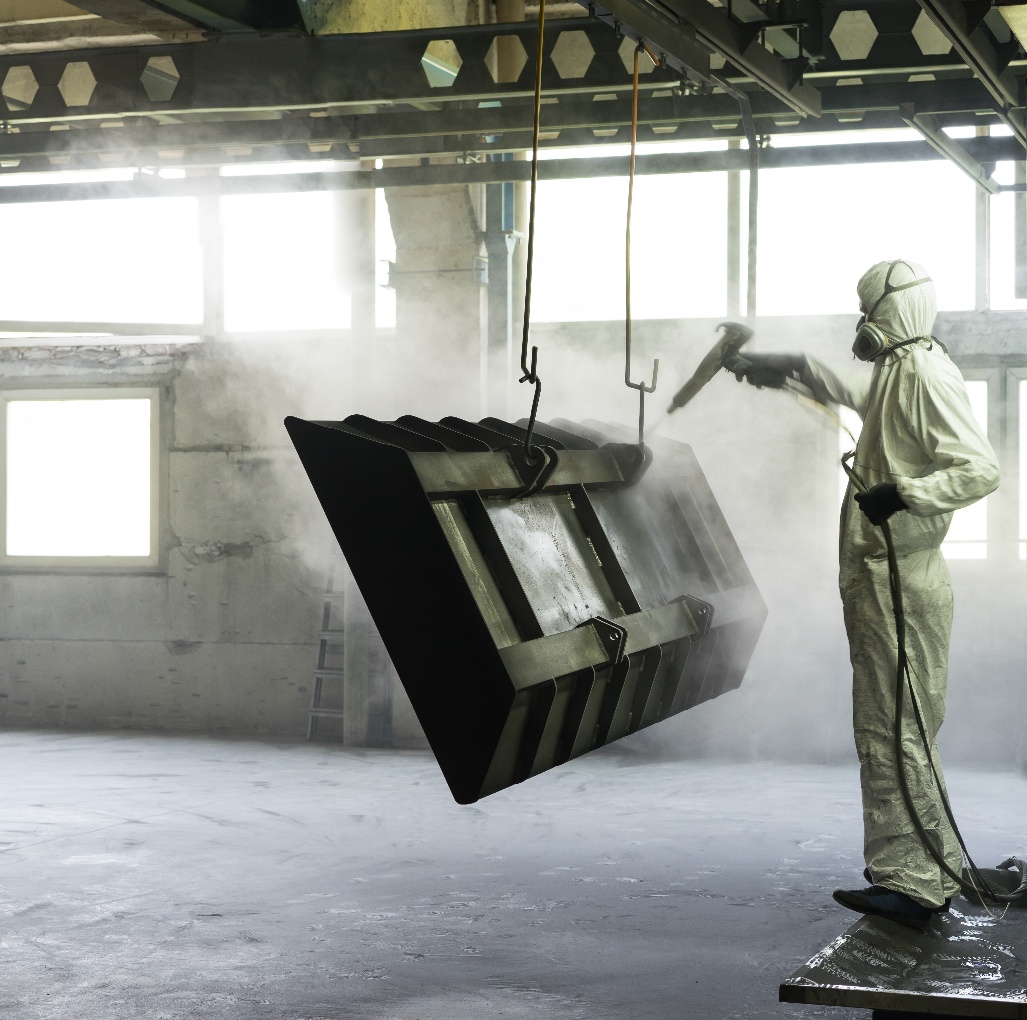
CLEAN AIR AND WHY QUALITY POWDER COATING DEPENDS ON IT
Powder coating is a dry coating process used as a metal finish mostly on industrial equipment. Powder coating is applied as dry powder through an electrostatic process then cured with heat. It is well known for providing high-quality finishes in terms of both functionality and overall look.
The powder coating finishes are not only sturdy but flexible as well. It can be used on different surfaces, including metal, concrete, steel, and plastic. It’s suitable for both indoor and outdoor applications, and it’s one of the most cost-effective finish options.
Contaminated air creates defects in the finished product, resulting in lost revenues and a damaged reputation.
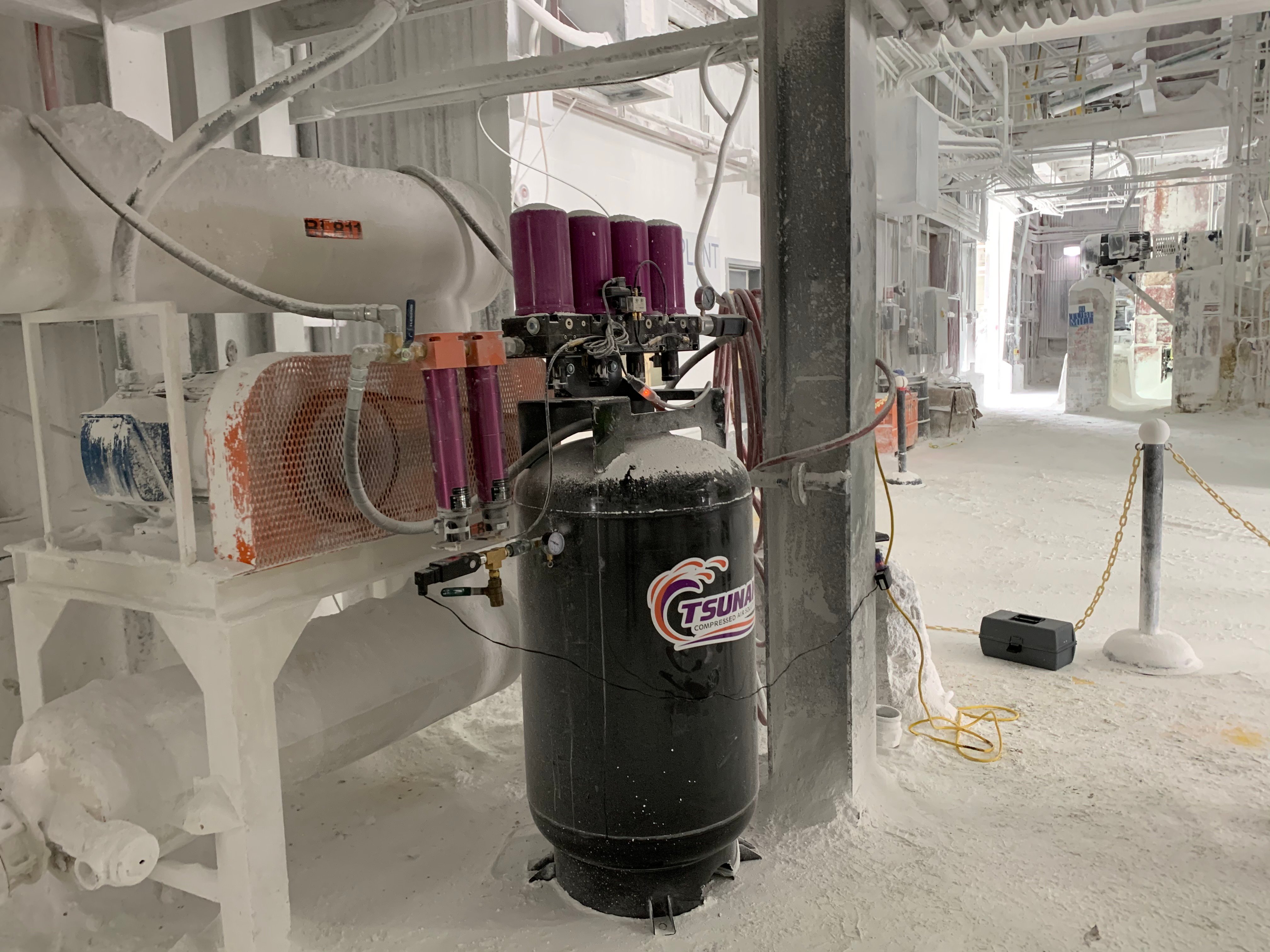
Dry Air as a CNC Machinery Performance and Lifespan Booster
Computer Numerical Control (CNC) Machines allow complex parts to be created with relative ease and for goals to be accomplished that were not previously possible. From a CNC lathe to a CNC milling machine, these completely different tasks increase manufacturing efficiency and capabilities.
Because CNC machines run in a manner that maximizes efficiency parts/widgets can be created with less waste and more accuracy, all in a shorter time frame. A CNC machine can accomplish three-dimensional cutting with a single set of directions!
To keep these CNC machines operating smoothly, dry air is necessary to reduce the risk of toll corrosion and to keep the exposed surfaces clear of debris. Compressed air also can be used to cool the machine to extend its lifespan - the less surface moisture exposed surfaces encounter, the less rust develops.
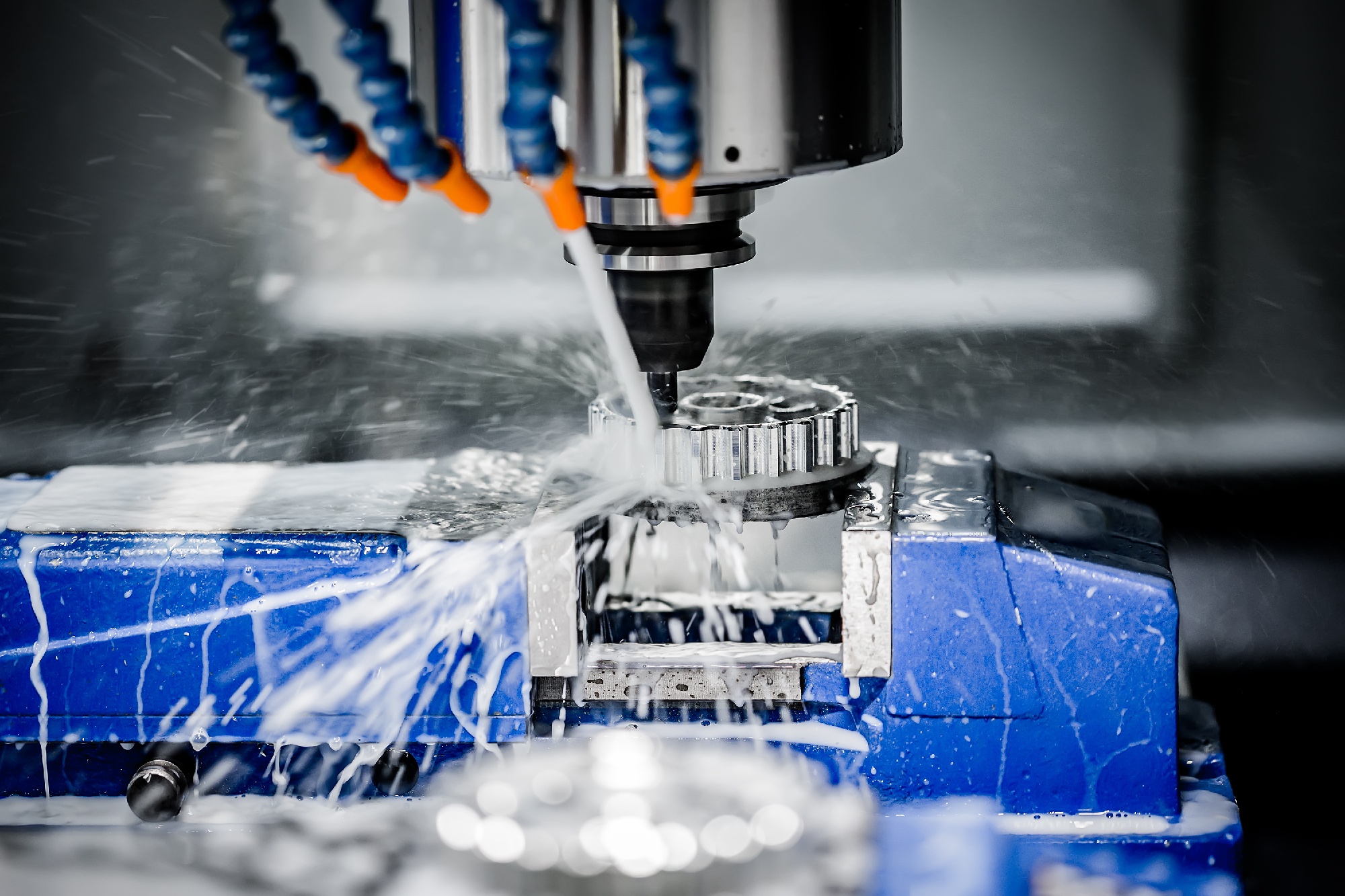
Laser Cutter Optimization and the Compressed Air Solution
Laser Cutters are a type of CNC Machine that uses a focused laser beam to cut through materials creating designs and patterns determined by a creator. Laser cutters are used to cut paper, cardboard, some plastics, and wood.
Clean, dry air assist is a common, money-saving technique for businesses that use laser cutters. The laser cutting process creates heat and debris, which can be dangerous to both the product and the business. Using air assist decreases the danger, increases efficiency, and cuts down on residue buildup to reduce time spent cleaning.
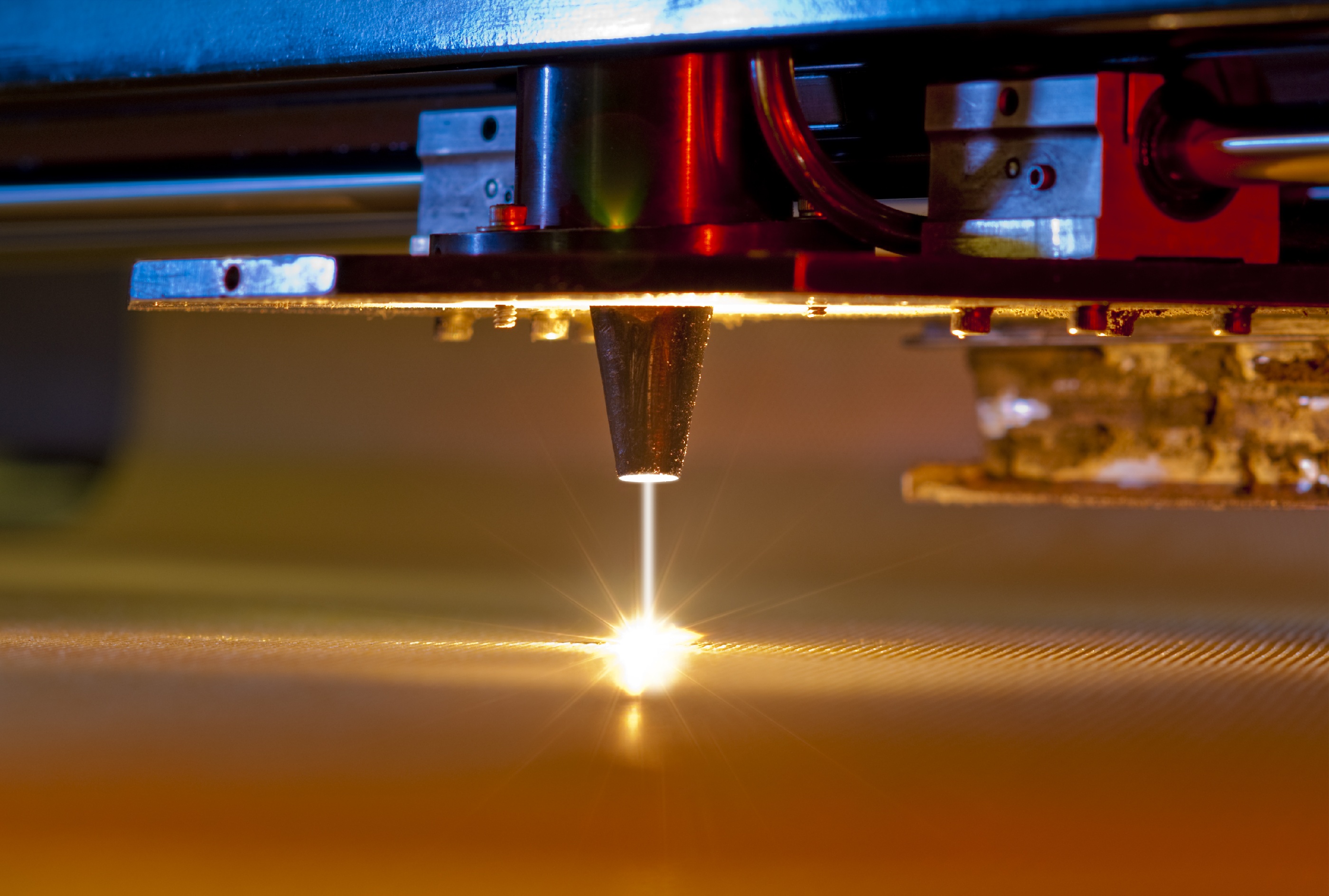