Learning Center
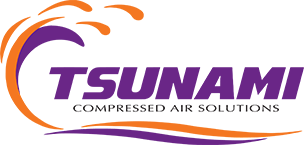
The Tsunami Learning Center is a wealth of resources compiled for your benefit. From the most recent blogs on compressed air quality and its benefits to videos explaining system components and installation, this page provides an answer to the questions we hear regularly.
Check out our FAQ section and our catalog and installation manuals. If you don’t find your answer there, in the video library, or in the blogs, don’t hesitate to contact our experts. This page is updated regularly to provide you with the latest information on compressed air systems.
Video Library
Tsunami’s Video Library offers a number of videos that explain how our compressed air systems work, the different types of drain valves available, and the service and replacement of parts within the system. We also have installation videos to help with not only system installation but also calibration and settings for your compressed air dryer and related components.
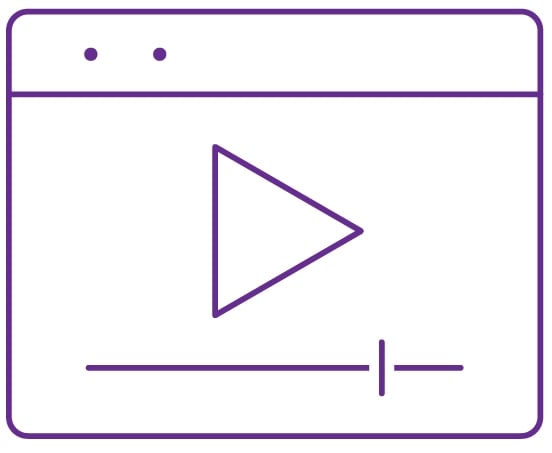
Common FAQ
-
When should you use a compressed air dryer?
Air dryers should be used when you want to remove or reduce the humidity levels in your compressed air system to meet or exceed the air quality requirements for the compressed air demands of your tools, equipment, or applications.
-
What is “dew point”?
Dew point is the temperature where air is saturated with water and moisture will begin to condense. In other words, it’s the point where condensation (dew) begins to form. Dew point is always stated as a temperature and is most common measurement of compressed air water content.
-
What is the difference between pressure dew point vs. atmospheric dew point?
In compressed air applications, pressure is critical when discussing dew point. Compression and expansion of air affects its dew point. Generally speaking, compression increases dew point, and de-compression lowers dew point. For this reason, the phrase Pressure Dew Point (PDP) is commonly used. This term refers to the dew point of the compressed air at full line pressure. On the other hand, Atmospheric Dew Point refers to what the dew point would be if fully depressurized to atmospheric conditions.
.
-
How do you determine the dew point suitable for your application when selecting a compressed air dryer?
The best and easiest way to determine this is by checking the equipment manual or by asking the manufacturer what the Pressure Dew Point (PDP) requirements are for your equipment. Another method is to calculate the dew point temperature. However, many industrial applications specify a pressure dew point of -40⁰ F/C at line pressure. This is often found in process industries, facilities where air lines will be exposed to cold ambient air, and systems where compressed air interacts with sensitive instruments and processes.
-
How do you calculate dew point temperature?
Determine the lowest ambient temperature your compressed air system will be exposed to by checking the location of air lines throughout air conditioned or unheated areas. Take that temperature number and lower it by 20°. This will give you dew point temperature needed to prevent condensation from forming.
-
What Is the Difference Between Air Filters and Air Dryers?
Air drying is the removal of water vapor (humidity) from compressed air. This can be done by using a desiccant, membrane, refrigeration, or deliquescent dryer. Air filtration uses specific filters to remove particulates, water, oil droplets, and aerosols. These are to be removed by the filters before entering the dryer. Ideally, filters and dryers work together to produce clean, dry air for your application.
-
Where Do You Place Your Compressed Air Filters?
The further away from the compressor, the more effective your filtration will work. For water separators, place them at all air tool drops with regulators. It is recommended to use the filters in front of the air dryer to act as pre-filters. Placing filtration closest to the inlet side of an air dryer will allow for optimal performance and longevity of the drying unit.
-
What Is the Difference Between Coalescing and Particulate Filters?
Both filters perform similarly in cleaning out contaminates but with opposite air flow. Coalescing filters have an air flow going to the center of the element with the air filtering towards the outside. The contaminates exit through the sides and drain to the bottom of the filter. Particulate filters flow opposite. In this element, the air flow is going down the sides of the filter and sending contaminates to the center.
-
Why Does My Air System Need a Drain?
Neglecting to consistently drain condensate and contamination will result in endless headaches and costly downtime. Inadequate or forgotten draining dramatically wears on filtration systems causing them to become ineffective and damaging to critical equipment and processes. There are a variety of drain styles to assure timely and effective draining for your facility.
-
What is the difference between float, pneumatic, and electronic drains?
Float drains contain a float within the device that normally seats on a small orifice. When liquid enters the drain the float rises off its seat, exposing the orifice and allowing liquid to discharge through the stem. As the liquid level drops, the float re-seats and seals the orifice. These drains operate only when a sufficient quantity of condensate is present. Usually, a manual override is provided which allows for drainage of the system on demand or during cleaning. Most float-operated drain valves leave a small amount of condensate in the reservoir when discharging, this prevents the loss of valuable compressed air.
Electronic drains incorporate a solenoid valve and an electric timer with two on/off settings. ON is the setting for the amount of time the valve needs to stay open (0.5 to 10 seconds) and OFF is the time between openings (0.5 to 45 minutes). The two settings need to be adjusted to the size of the compressed air system in such a way that all condensate is discharged with a minimum loss of air. This can be fined tuned based on the system. It is also highly recommended to use an inlet strainer on the solenoid valve to prevent debris from fouling.
Pneumatic drains are simple and robust. An external condensate reservoir collects liquid. When the liquid rises to a set point a mechanical switch sends pilot air to an air cylinder that opens a ball valve, draining the reservoir and returning the piston to a relaxed position. The ball check closes preventing zero pressure loss in the system. The drain port opens and the stored condensate is ejected. No compressed air is wasted in the process, except for the tiny amount of pilot air.
Catalogs & Installation Manuals
Tsunami offers a full product catalog so you can find the product you are looking for, and this page also has installation manuals for our systems and components.
From an Ultra Series Wall Mounted Dryer to a Moisture Minder Drain or a CFM Test Kit, we have an installation manual to help you if you run into an issue.
Don’t forget to check out our Video Library as well, where our experts walk you through the steps of installing Tsunami Compressed Air Systems and the different filters we offer.
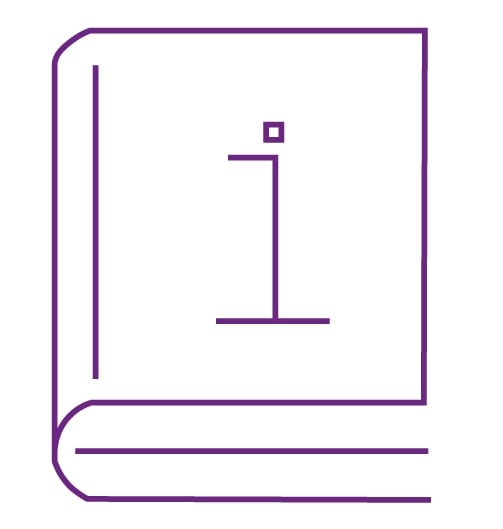
What is an Aftercooler and is it Crucial for Compressed Air Systems?
Introducing the Tsunami Aftercooler
Benefits of Point-Of-Use For Compressed Air Dryers
The Importance of Humidity Control with Regenerative Dryers in Industrial Applications
Industrial Air Dryers for the Oil & Gas Industry: Why You Need One
The Portable Pure-5T is fantastic! It is exactly what you need for for challenging an air supply problem. I used it for an install and proved to the customer that it was their poor air quality causing the poor paint job.
It been a year since we talked and I ordered from you, your Model 150-4 Auto Oiler Kit to install on my 2002 Gehl 2480 Round Baler. The install was straight forward and it works great.
For over 8 years Tsunami has taken care of all of my needs and your customer service has been off the charts! I can’t express enough how appreciative I have been throughout the years and value our simple business relationship.
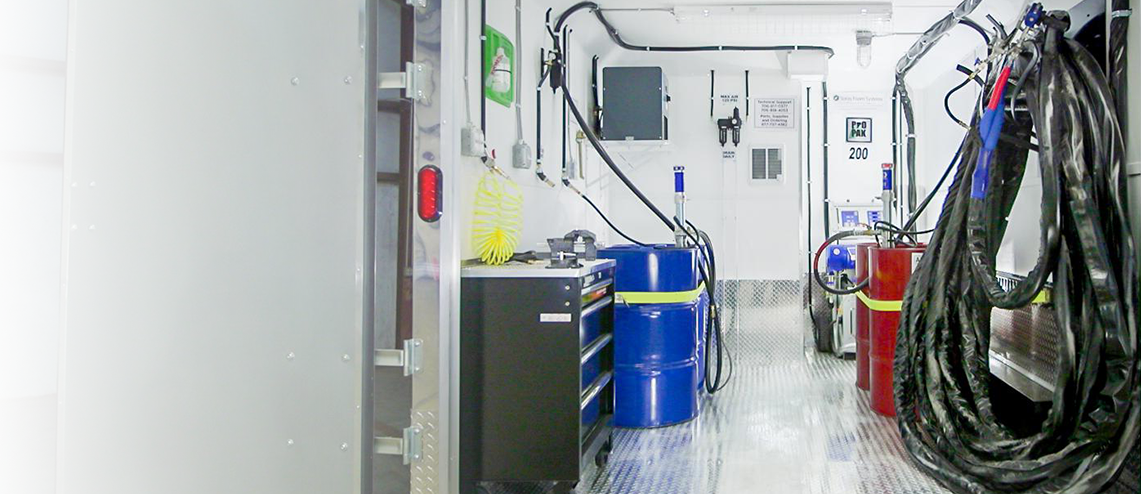