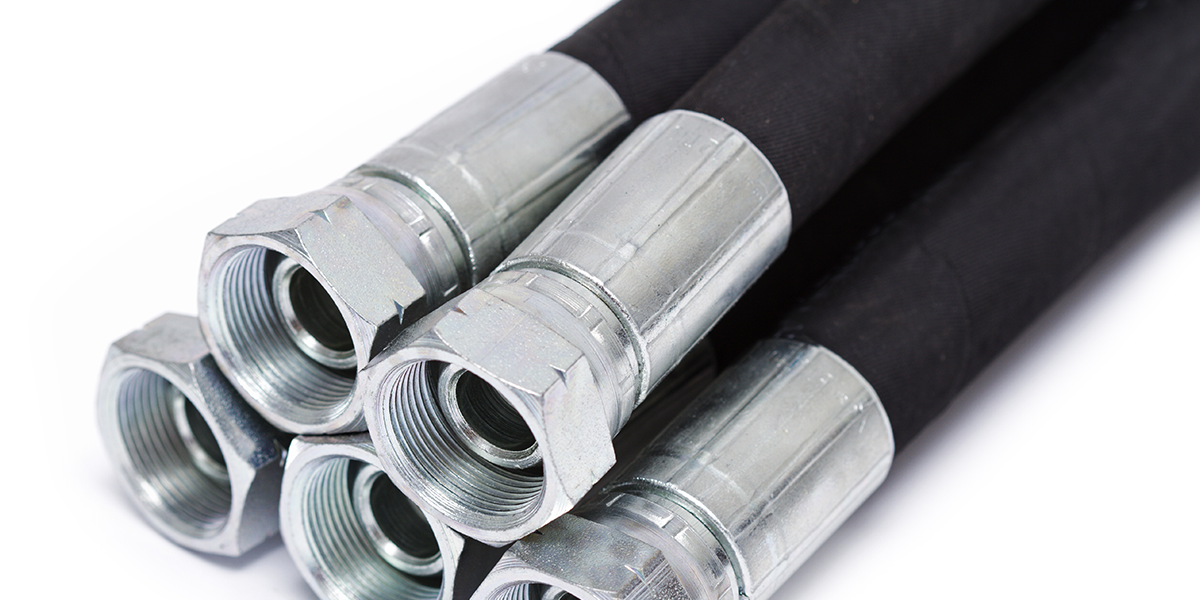
Hydraulic hoses are essential components in many industrial and commercial applications but they can be dangerous if improperly handled.
Hydraulic hose failure is one of the most common causes of workplace accidents and injuries, making it important to understand the answer to “why do hydraulic hoses fail?” Likewise, you can discern the reasons associated with these components and how to prevent failure.
With proper maintenance and safety protocols in place, you’ll be able to reduce downtime due to failed hoses as well as protect operators from serious harm.
10 Reasons Hydraulic Hoses Fail On the Job
On-the-job safety training is important to reduce the danger to those who are focused on getting the job done. Hydraulic hoses are important to the overall job progress, but proper maintenance is key, and all too often, overlooked.
Understanding what leads to a hose malfunctioning or bursting allows you to help those in need take steps to ensure that equipment operates safely at all times. There are a variety of potential reasons why hydraulic hoses can fail on the job, including:
-
Abrasion
-
Incompatible fluid
-
Twisting
-
Defective hose
-
Coupling issues
-
Operating conditions
-
Bending in multiple locations
-
Poor workmanship
-
Old age
-
Contamination
1. Abrasion
Abrasion is a common issue on the job site. Hoses are exposed to wear and tear due to rough conditions during their useful life. As such, they may become worn down over time leading to cracks in the rubber material or even holes in the outer casing.
This type of damage can occur due to a variety of factors, including contact with other objects, exposure to harsh chemicals or extreme temperatures, and even physical trauma from an outside force. Extended abrasion can eventually cause hydraulic hoses to fail, leading to serious accidents or injuries.
It’s important for employers and workers alike to be aware of this potential risk so that any issues are caught early before more extensive damage can occur. Abrasion generally occurs over a period of time as opposed to instantaneously; therefore it's important for regular inspections of all equipment and components used at work sites.
2. Incompatible Fluid
When a hose is used with a fluid that is too thick or viscous for it, this can lead to excessive wear and tear as well as catastrophic rupture. It’s important to make sure that all hoses are compatible with the fluids used in order to prevent premature failure.
3. Twisting
When hoses are twisted during installation, it can lead to kinks and weakened spots in the hose material. Eventually, this state causes the hose to fail under pressure. This type of damage can be difficult to spot until it’s too late, so it’s important for employers and workers alike to take steps toward prevention of the issue occurring in the first place.
Twisting should always be avoided when installing or replacing a hydraulic hose, as even small amounts of torque applied on the end fittings can add up over time and weaken the hose itself.
4. Defective Hose
Hoses that are poorly designed or manufactured are more prone to damage, leading to serious harm. This type of damage is particularly hazardous as it can occur without any warning signs or symptoms.
A defective hose could cause serious harm on the job site including:
- Injuries to workers
- Damage to equipment
- Lost time due to repairs and inspections
5. Coupling Issues
A coupling is a critical component of a hydraulic hose, connecting two pieces together and allowing for the transfer of fluid. If the couplings are incorrectly installed or worn out, it can lead to a number of issues including:
- Leaks
- Reduced system pressure and efficiency
- Hose bursts under pressure
Leaks can contribute to reduced system pressure and efficiency, leading to increased wear and tear on the hoses. While fixing your immediate issue will resolve things for now, further trouble could be looming in the future.
6. Operating Conditions
When the temperature or pressure of a hose exceeds its design limits, it can cause the rubber material to become brittle and crack.
The same is true for hoses exposed to sudden drops in temperature; these components are particularly susceptible to thermal shock which can also lead to rupture.
The Diamondback and Diamondback Pro Sleeves have been tested to withstand temperatures of 200°F continuously and up to 350°F of intermittent exposure. They have also been tested to withstand over 1.7 million abrasion cycles.
Want to Learn More?
Check out our blog on the Line of Sight Standards as well.
7. Bending in Multiple Locations
One of the most dangerous causes of hydraulic hose failure is when hoses are bent in multiple locations along their length. This can occur due to improper installation or routing which weakens the hose material as well as increases operating pressure.
It's also important to note that exceeding the minimum bend radius for a given hose can cause it to kink, leading to cracks and tears in its walls which will eventually result in failure. To prevent this from happening, it’s essential that all hoses be routed correctly with enough slack so they don't have too many bends or twists. Additionally, care should be taken not to exceed the minimum bend radius specified by the manufacturer for each type of hose.
8. Poor Workmanship
Issues with poor workmanship can include:
- Incorrect routing
- Exceeding the minimum bend radius for a given hose
- Twisting during installation
- Not properly securing couplings or connections
All of these issues can lead to dangerous leaks or ruptures which in turn can cause serious harm if not caught.
9. Old Age
As hoses are exposed to the elements and are subjected to repeated stress on rough ground or via heavy site traffic throughout their useful life, they can become brittle and crack.
With proper maintenance protocols in place, you can reduce downtime due to hazardous failures caused by old age and protect operators and equipment from harm.
10. Contamination
Hydraulic hose failure due to contamination is one of the most overlooked causes of workplace accidents and injuries. Contamination can occur in various ways:
- Foreign materials entering the system through improper installation or lack of hose cleaning prior to installation
- Improper maintenance
- Other component breakdown such as pump wear and tear or valve wear and tear
If not addressed quickly, contamination can lead to reduced system efficiency and even catastrophic rupture. It’s important for employers and workers alike to understand how contamination affects hydraulic hoses so that any issues can be caught before more extensive damage has occurred.
Diamondback is Your Answer
Numerous workplace accidents and injuries have been attributed to hydraulic hose failure. Instead of asking “why do hydraulic hoses fail?” ask yourself: “what can be done on the job site to reduce the risk?”
Diamondback, Diamondback Pro, and Diamondback Lite sleeves not only stand up to high temps and abrasion, but they also provide:
- Flexibility
- Chemical resistance
- UV protection
In terms of reliability, Diamondback and Diamondback PRO sleeves can provide protection from pinhole leaks up to 4,000 PSI and can mitigate spillage from pinhole leaks that occur. These two sleeves can also protect from bursts up to 12,000 PSI.
Make Safety Your First Priority
Learn more about materials for protective sleeves and weigh your options for a safer setup on your client’s job site by contacting the Python Team today.