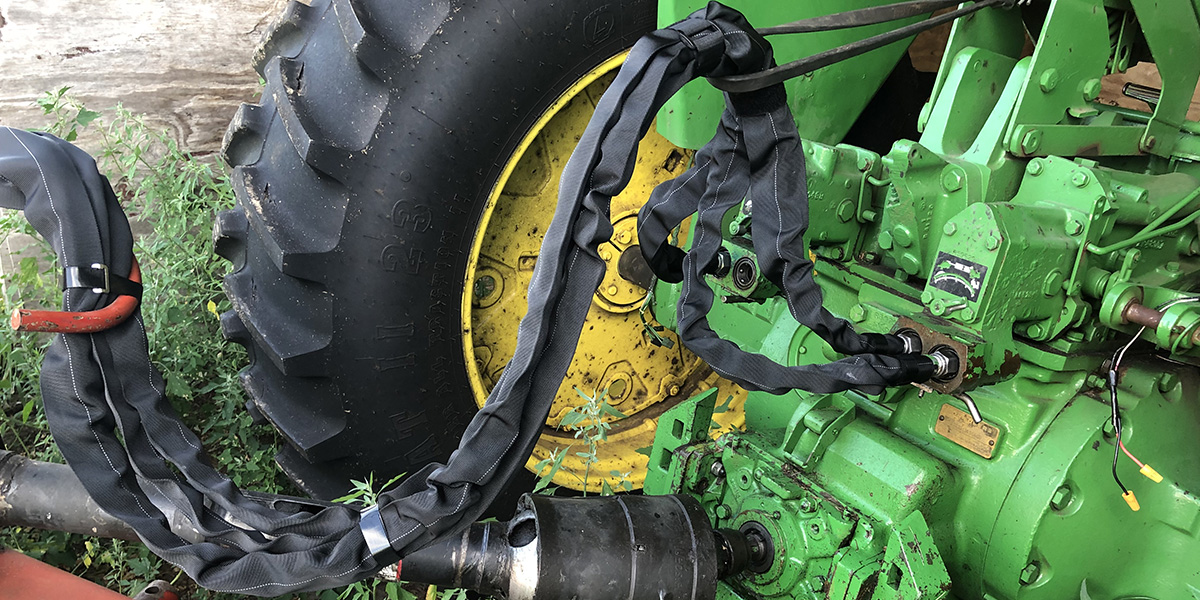
From a mining operation to a construction project, hydraulic hose failure on equipment happens more frequently than most operators care to admit.
When a hydraulic hose fails, it’s not just the equipment that can be damaged – the operator and anyone near the machine can suffer injury or even death. A compromised hydraulic hose creates a host of issues, from a line bursting, causing machine damage, to a pinhole leak spraying hot hydraulic fluid.
Table of Contents:
1. 3 Common Causes of Pinhole Leaks, Bursts, & Their Solutions
2. How to Protect Hydraulic Hoses & Equipment Operators: Proactive Measures
3. Protecting Hydraulic Hoses & The Python Advantage
Pinhole leaks are one of the most common reasons hydraulic hoses malfunction. Small, barely visible to the naked eye, and often tough to locate, a pinhole leak can cause big problems. Bursts, a much bigger and more apparent display of an issue with the line, do the same.
The best way to prevent pinhole leaks and bursts is to understand the common causes and implement measures to protect the integrity of the hydraulic hose.
3 Common Causes of Pinhole Leaks, Bursts & Their Solutions
Before determining whether the hydraulic hoses sleeve or wrap is providing adequate protection, it’s important to understand how (and why) the hose could burst or leak.
While there are several situations that can cause a pinhole leak or hose burst, there are three common causes:
- Abrasion
- High temperatures
- Incorrect hose routing
1. Abrasion
Abrasion occurs when a hydraulic hose rubs, expands and contracts against the machine during operation as the pressure changes within the hose.
Effect: This repeated contact causes the outer layers of the hose to slowly deteriorate, weakening it and eventually resulting in a leak or burst.
Solution: Make sure the hose is not in contact with any surfaces and equip it with a protective cover. The best hydraulic hose protection sleeves meet ISO 6945 and ASTM D6770 and are tested to provide next-level abrasion protection for more than 1 million cycles.
2. High Temperatures
When hoses are exposed to high temperatures, they begin to lose their flexibility, stiffen, and crack.
Effect: As time goes by, hose cracks may eventually reach the outside of the hose, causing bursts or pinhole leaks.
Solution: Install a heat-resistant sleeve, such as the Fire-Sleeve, around the hose. In addition, inspect the hose for proper assembly and the appropriate amount of fluid.
3. Incorrect Hose Routing
The routing of hydraulic hoses directly impacts their lifespan. When routed through a highly-abrasive area, such as next to the engine compartment, the hose is exposed to additional wear and tear.
Effect: Incorrectly routed hydraulic hose systems face a number of issues:
- Surface damage
- Bends
- Rubbing
- Kinks
Left unaddressed, these issues compound and result in pinhole leaks or hose bursts.
Solution: Reroute hoses away from an abrasive area, pivot point, or high-temperature environment. Pay close attention to make sure the minimum bend radius is met to avoid failure.
How to Protect Hydraulic Hoses & Equipment Operators: Proactive Measures
Though there are many causes for a hydraulic hose to spring a pinhole leak or burst, there are steps that help prevent issues in the first place.
Partnering with a state-of-the-art protective sleeve manufacturer is critical to ensuring the hydraulic system on your machine or equipment is connected and routed correctly.
Once a hydraulic hose is cut to the proper length, it must be cleaned and flushed to eliminate internal contamination by debris. The inner tube should be clean and the ends of a hydraulic hose should be clamped after the fittings have been crimped into place.
Hydraulic hose pinhole leaks act much like a hypodermic needle, piercing the skin and injecting hydraulic fluid into nearby people.
Pinhole skin penetration can occur at pressures as low as 100 psi, take precautions when working around hydraulic hoses by using PPE (glasses, gloves, etc.). Most importantly: never use your hands to check for hydraulic leaks.
In addition to wearing protective equipment, it’s important to incorporate a hydraulic hose protective sleeve to machinery with both abrasion resistance and line-of-sight operator protection, such as Python’s Diamondback series.
Python’s Diamondback sleeves are pinhole tested to 4,000 psi and burst tested to 12,000 psi. In addition to line-of-sight protection, Diamondback sleeves are also tested for colorfastness through the Zenon Arc testing.
The Diamondback sleeve is also tested to meet standards such as:
- ISO 6945
- ASTM D6770
- EU Machinery Directive 2006/42/EC
- NSWs “Guidelines for Fluid Power Systems Safety at Mines”
Protecting Hydraulic Hoses & The Python Advantage
Ensuring protective sleeves are integrated onto your machine’s hydraulic hoses can prevent damage to the machine and injury to the operator.
Python also offers a full range of protective sleeves and wraps to accommodate a wide range of industries including:
- 1050 Ballistic Nylon
- 1050 Radiant Lined/5601 Radiant Lined
- Fire Sleeves
- Therma Sleeve
- Weld Shield
- & many more
Upgrade Your Hydraulic Hose Protection
Have questions about how Python’s protective solutions keep your workers safe and equipment functioning? Contact us today and our team of experts will walk you through your decision-making process to ensure you’re getting the best sleeve possible for your application.